Understanding Special 3D Printing Materials
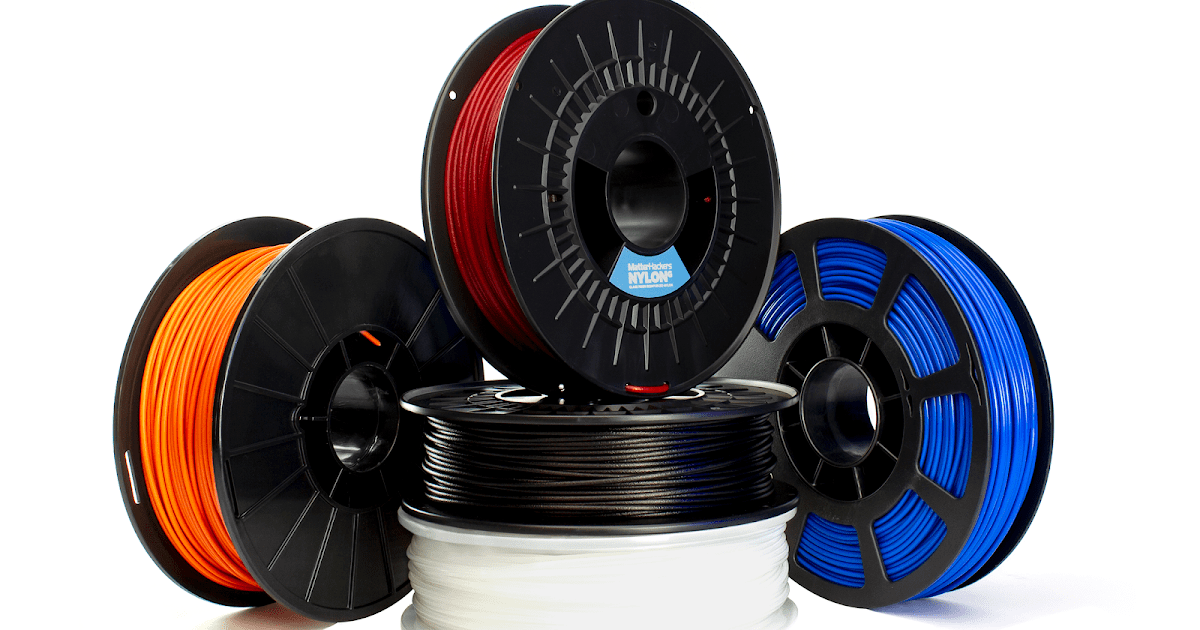
Specialty materials in 3D printing unlock possibilities that standard materials can’t achieve. While these special 3d printing materials often require more expertise and specialized equipment, their unique properties make them essential for specific applications across various industries.
Material Quick Reference Table
Material | Min. Wall Thickness | Resolution | Price | Best For | Key Features |
---|---|---|---|---|---|
TPU-95A | 2.0mm | ±0.4mm | Higher | Flexible Parts | Elastic, Durable |
ASA | 2.0mm | ±0.4mm | Medium | Outdoor Use | UV Resistant |
PVA | 2.0mm | ±0.4mm | Higher | Support Material | Water Soluble |
Carbon Fiber Composites | 2.0mm | ±0.4mm | Premium | Performance | Lightweight, Rigid |
Glass Fiber Composites | 2.0mm | ±0.4mm | Higher | Flexible, Lower Cost | Flexible, Durable |
ESD Composites | 2.0mm | ±0.4mm | Medium | Electronics | Static Dissipation |
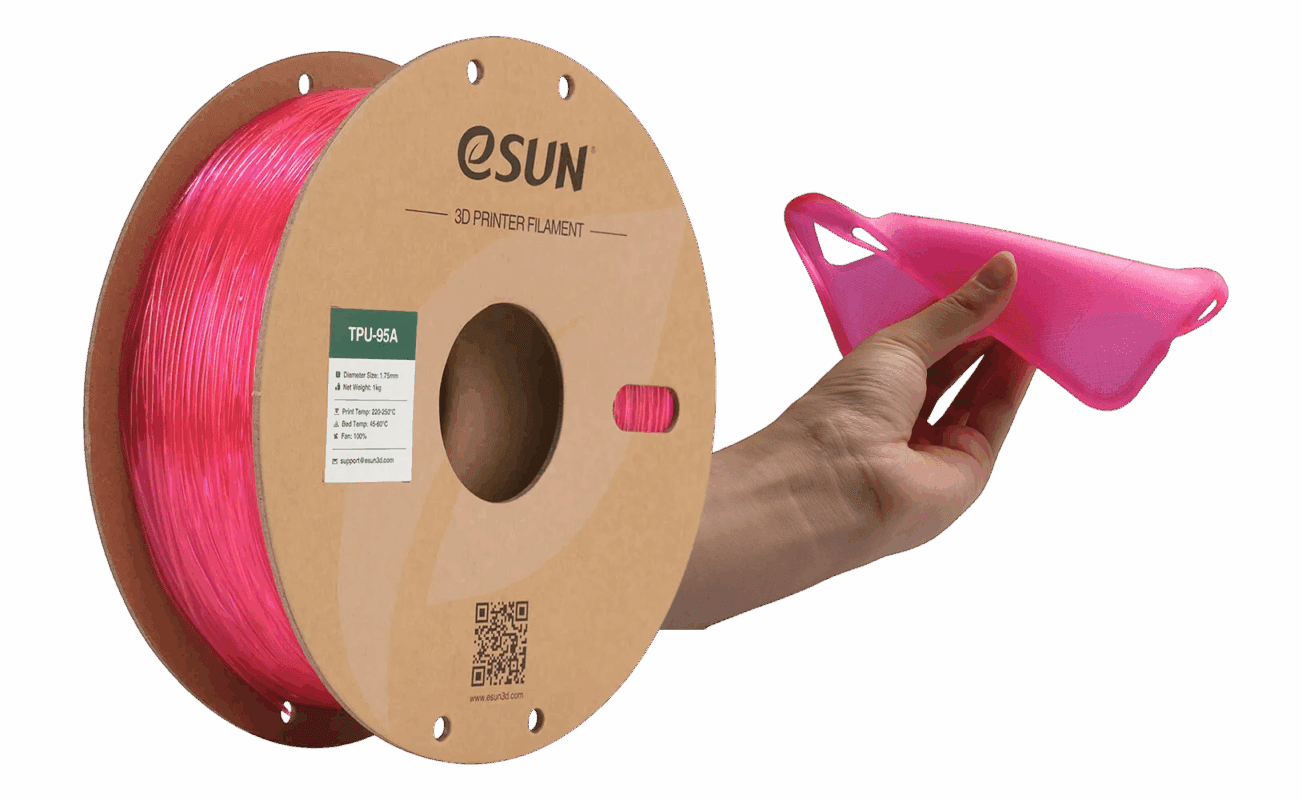
TPU-95A: Mastering Flexibility
TPU-95A stands out in the world of 3D printing materials for its unique combination of flexibility and durability. This material opens up possibilities for parts that need to bend, stretch, or compress while maintaining structural integrity. Understanding its characteristics is crucial for successful implementation in various projects.
Technical Properties:
- Shore hardness: 95A
- Print temperature: 220-235°C
- Bed temperature: 60-80°C
- Elongation at break: 450%
- Minimum wall thickness: 1.2mm
Ideal Applications:
- Automotive gaskets and seals
- Protective cases and covers
- Custom shoe insoles
- Flexible hinges
- Vibration dampeners
Engineers often choose TPU-95A for projects requiring:
- Impact absorption
- Customized grip surfaces
- Compression resistance
- Weather sealing
- Wear resistance
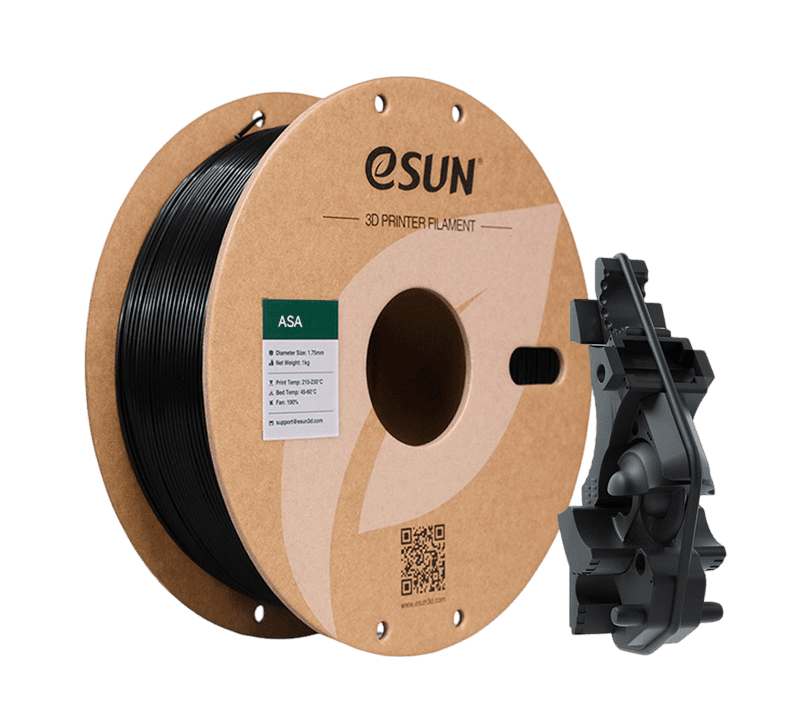
ASA: The Outdoor Performer
ASA (Acrylonitrile Styrene Acrylate) has established itself as the premier choice for outdoor applications. Its exceptional UV resistance and weather stability make it perfect for exterior components that need to maintain both appearance and structural integrity under harsh conditions.
Material Characteristics:
- UV resistance: Excellent
- Weather stability: Superior
- Impact strength: High
- Heat deflection: 95°C
- Color stability: Long-term
Common Uses:
- Outdoor enclosures
- Marine components
- Exterior fixtures
- Garden equipment
- Architectural elements
The material particularly excels in:
- Maintaining color under sunlight
- Resisting weather degradation
- Handling temperature fluctuations
- Providing structural stability
- Offering professional finish
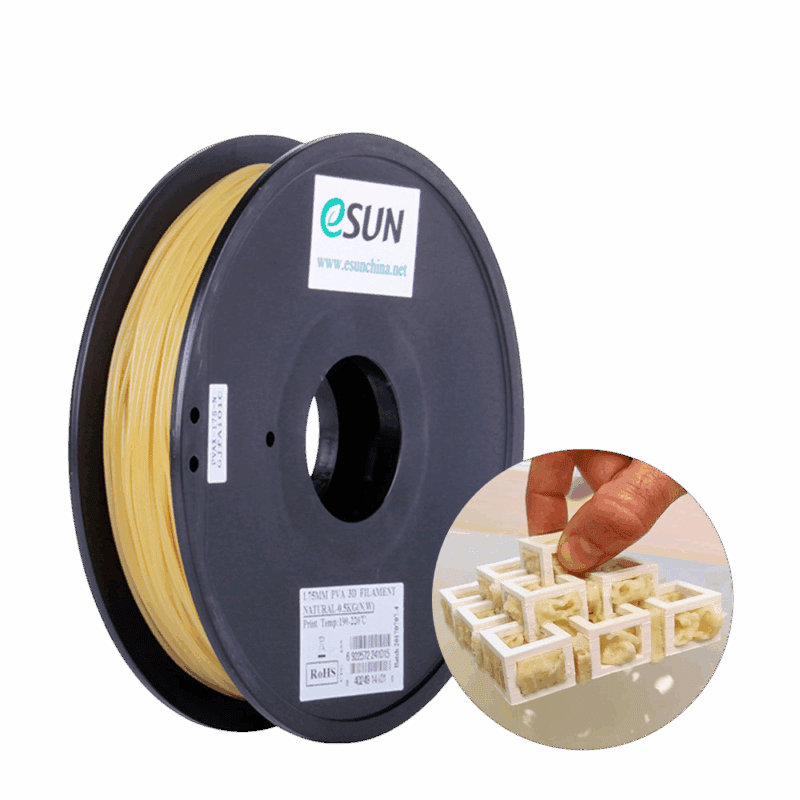
PVA: Support Material Specialist
PVA (Polyvinyl Alcohol) revolutionizes the creation of complex geometries through its unique water-soluble properties. This material serves specifically as a support structure that dissolves cleanly in water, leaving no residue on the primary print.
Technical Specifications:
- Dissolution rate: Fast
- Print temperature: 185-200°C
- Storage requirements: Strict
- Layer adhesion: Excellent
- Environmental impact: Low
Best Used For:
- Complex overhangs
- Internal cavities
- Intricate geometries
- Delicate structures
- Multi-material prints
Support structure considerations:
- Water temperature affects dissolution
- Proper storage prevents degradation
- Humidity control is crucial
- Clean dissolution process
- Environmental disposal

Carbon Fiber Composites: Engineering Excellence
Carbon fiber reinforced filaments represent the pinnacle of strength-to-weight ratio in 3D printing materials. These composites offer exceptional stiffness and dimensional stability, making them ideal for high-performance applications where weight and strength are crucial factors.
Material Benefits:
- Tensile strength: Superior
- Weight reduction: 25-30%
- Dimensional stability: Excellent
- Heat resistance: High
- Layer adhesion: Strong
Industrial Applications:
- Aerospace components
- Performance automotive parts
- Industrial tooling
- Robotics frameworks
- Structural elements
Engineering considerations include:
- Hardware requirements
- Print temperature stability
- Bed adhesion methods
- Cooling strategies
- Post-processing needs
Filament Properties (eSun), Carbon Fiber Series
Materials | PLA-CF | PETG-CF | ABS-CF | PA-CF |
Tensile Strength (MPa) | 39 | 28 | 29.9 | 140 |
Elongation at Break (%) | 4.27 | 3.6 | 5.7 | 10.61 |
Flexural Strength (MPa) | 103 | 80.8 | 76.2 | 140 |
Flexural Modulus (MPa) | 5003 | 2500 | 2694 | 4363 |
Heat distortion Temperature (℃) | 53 | 70 | 94.9 | 155 |
UV Protection | None | High | None | None |
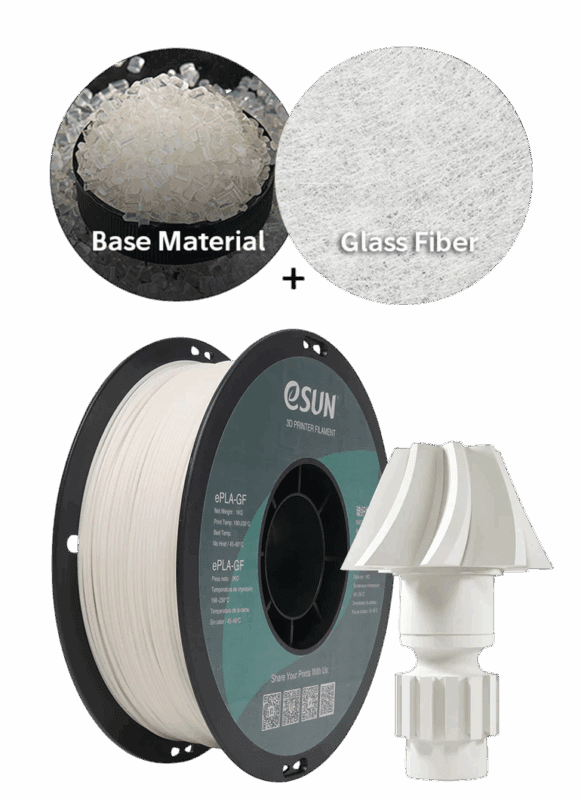
Glass Fiber Composites: Cost Effective Performance
Glass fiber reinforced filaments offer high durability and impact resistance in 3D printing, combining flexibility with strength. These composites are a popular choice for parts that must withstand wear and tear while keeping costs manageable.
Material Benefits:
- Tensile strength: High
- Impact resistance: Excellent
- Dimensional stability: Good
- Cost-efficiency: High (When comparing with Carbon Fiber Composites)
- Color options: Versatile
Industrial Applications:
- Automotive brackets and housings
- Construction tools and jigs
- Electronics enclosures
- Marine components
- Sports and outdoor gear
Engineering considerations include:
- Nozzle durability
- Print temperature adjustments
- Bed adhesion techniques
- Cooling settings
- Surface finishing
Filament Properties (eSun), Glass Fiber Series
Materials | PLA-GF | PETG-GF | ABS-GF | PA-GF |
Tensile Strength (MPa) | 59.27 | N/A | 51.3 | 76.93 |
Elongation at Break (%) | 7.99 | N/A | 6.1 | 21.07 |
Flexural Strength (MPa) | 85.01 | N/A | 84.6 | 77.75 |
Flexural Modulus (MPa) | 4414.8 | N/A | 2346.9 | 1714.6 |
Heat distortion Temperature (℃) | 56 | N/A | 92.7 | 120 |
UV Protection | None | N/A | None | None |
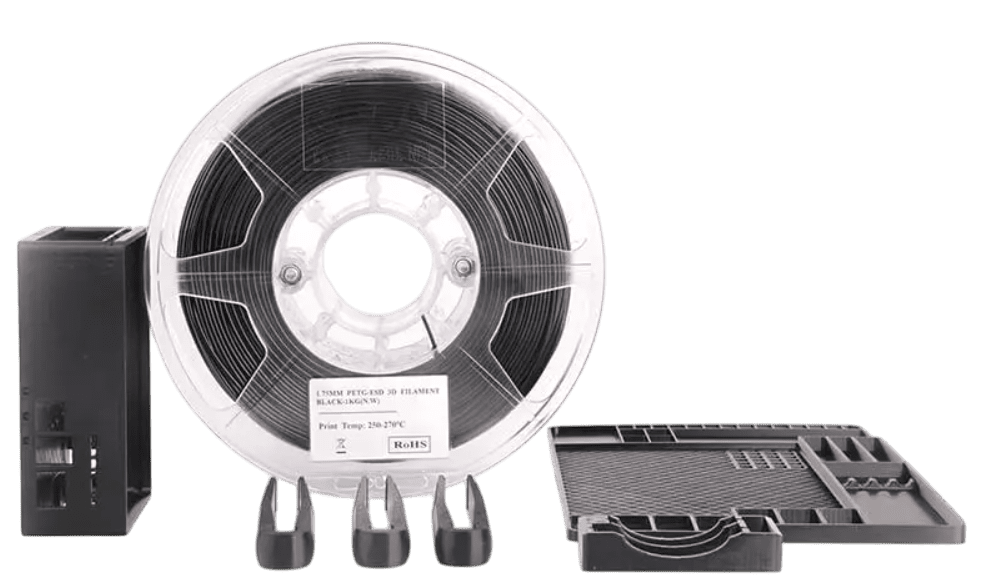
Electrostatic Discharge (ESD) Composites: Protecting Sensitive Electronics
ESD (Electrostatic Discharge) filaments are specially designed for 3D printing applications that require the prevention of static electricity build-up. These composites provide conductive or dissipative properties, ensuring that printed parts can safely handle sensitive electronic components by minimizing the risk of electrostatic damage.
Material Benefits:
- Static dissipation: Excellent
- Dimensional accuracy: High
- Heat resistance: Moderate
- Layer adhesion: Strong
- Surface finish: Smooth and uniform
Industrial Applications:
- Electronics housings
- Jigs and fixtures for circuit boards
- Cleanroom tools and equipment
- Sensor enclosures
- Robotics parts in static-sensitive environments
Engineering considerations include:
- Print temperature and cooling settings
- Humidity control
- Bed adhesion techniques
- Nozzle and bed material compatibility
- Post-processing for optimal conductivity
Filament Properties (Smith3D – ESD Series)
Materials | ESD PETG | ESD ABS |
Tensile Strength (MPa) | 35~40 | 35~37 |
Elongation at Break (%) | 5~8 | 5~7 |
Flexural Strength (MPa) | 64~66 | 60~61 |
Flexural Modulus (MPa) | 1400~1500 | 1300~1500 |
Heat distortion Temperature (℃) | 65 | 98 |
UV Protection | High | None |
Technical Considerations and Best Practices
Success with specialty materials requires attention to specific technical details and proper preparation. Environmental control plays a crucial role in achieving consistent results.
Essential Printing Conditions:
- Controlled environment temperature
- Monitored humidity levels
- Clean printing surface
- Proper ventilation
- Regular maintenance schedule
Material Storage Requirements:
- Sealed containers usage
- Desiccant implementation
- Temperature monitoring
- Regular rotation practices
- Moisture prevention methods
Pre-Print Preparation
Proper preparation significantly increases success rates with specialty materials. Each material requires specific handling procedures and printing parameters.
Preparation Checklist:
- Material conditioning
- Printer calibration
- Test print execution
- Parameter verification
- Environmental checks
Quality Control Measures
Quality control becomes particularly important when working with specialty materials due to their specific requirements and applications.
Quality Assurance Steps:
- Visual inspection protocols
- Dimensional verification
- Functional testing methods
- Surface quality assessment
- Documentation practices
Conclusion
Specialty 3D printing materials continue to push the boundaries of what’s possible in additive manufacturing. While they require more attention to detail and often specialized equipment, their unique properties make them invaluable for specific applications.
Success Factors:
- Understanding material properties
- Following proper procedures
- Maintaining equipment
- Controlling environment
- Regular testing
Future Developments:
- New material composites
- Enhanced printing processes
- Broader applications
- Improved properties
- Advanced techniques
Remember that successful printing with specialty materials requires patience, attention to detail, and a thorough understanding of both the material properties and printing requirements. When properly executed, these materials deliver exceptional results that surpass standard materials’ capabilities.