At Smith3D, we’ve helped thousands of clients navigate these choices, from architects crafting detailed models to engineers developing functional prototypes. This comprehensive guide draws from our real-world experience to help you make informed decisions about available colourful 3D Printing Options.
Understanding Multi Material vs Multi Colour
In the world of 3D printing, “multi-material” and “multi-colour” are often used as buzzwords, but they actually represent different technologies, different capabilities, and different end goals.
Understanding the distinction is critical if you want the best results for your projects, whether you’re a hobbyist, engineer, product designer, or entrepreneur.
In this guide, we’ll explore:
- How multi-colour and multi-material printing really works.
- What kind of hardware supports them best.
- Real-world examples using two top machines: the Bambu Lab H2D and Prusa XL.
By the end, you’ll know exactly what type of printer you need, and how to get the most out of it!
Simple Key Comparisons

Multi-Material
Involves two or more independent toolheads, each with its own hotend and usually its own extruder.
- Dedicated Toolhead per Material/Colour
- Each toolhead is responsible for one specific filament (material or colour), allowing for true multi-material or multi-colour printing with minimal cross-contamination.
- Independent Motion (on IDEX systems)
- Some printers (e.g., IDEX – Independent Dual Extruder) allow each toolhead to move independently, reducing issues like oozing and enabling duplication/mirror modes.
- Minimal Filament Travel
- Because the extruder is mounted close to or on the toolhead (usually direct drive), the filament path is short, reducing the chance of buckling or delays during extrusion especially with flexible filaments.
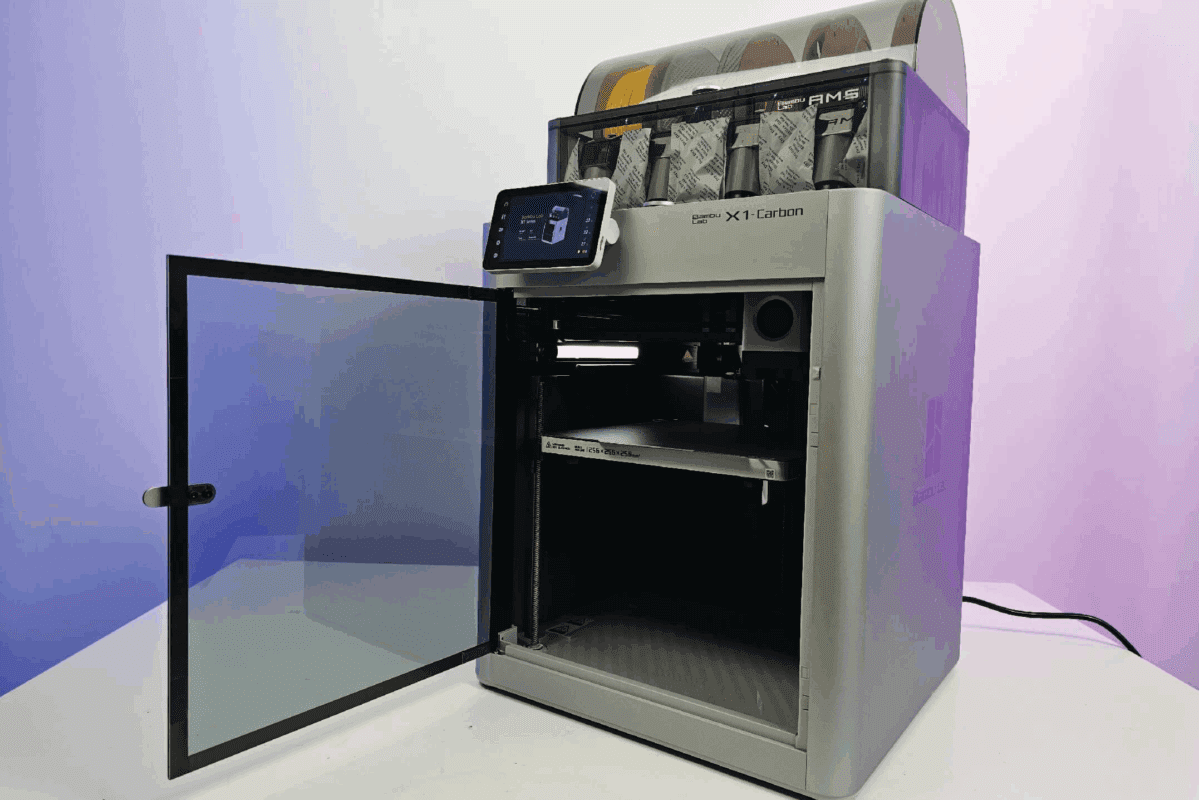
Multi-Colour
Uses a single toolhead to print with multiple filaments by relying on an external accessory system that manages filament switching.
- Single Hotend, Multiple Inputs
- Only one nozzle is used to extrude all filaments. The system relies on an accessory (like a filament switcher or selector) to change filaments during a print.
- Accessory-Reliant (e.g., Palette, AMS)
- Systems like the Mosaic Palette, or Bambu Lab AMS manage and splice or switch filaments externally before they reach the toolhead.
- Long Filament Path
- The filament travels a long distance from the accessory to the extruder, which can cause:
- Increased chances of filament buckling
- Slower switching times
- Wasted filament during purging (often in a purge block)
- The filament travels a long distance from the accessory to the extruder, which can cause:
Simple Comparison
Features | Multi-Material | Multi-Colour |
---|---|---|
Toolhead Count | Multiple | One |
Filament Switching | Tool-head independant | Accessory-controlled switch/splice |
Filament Path Length | Short | Long |
Buckling Risk | Low | Moderate / High |
Purge Waste | Minimal | Moderate / High |
Application | Multi-material, professional setups | Multi-colour, hobbyist & mid-range |
Comprehensive Comparison: Multi-Material vs. Multi-Colour
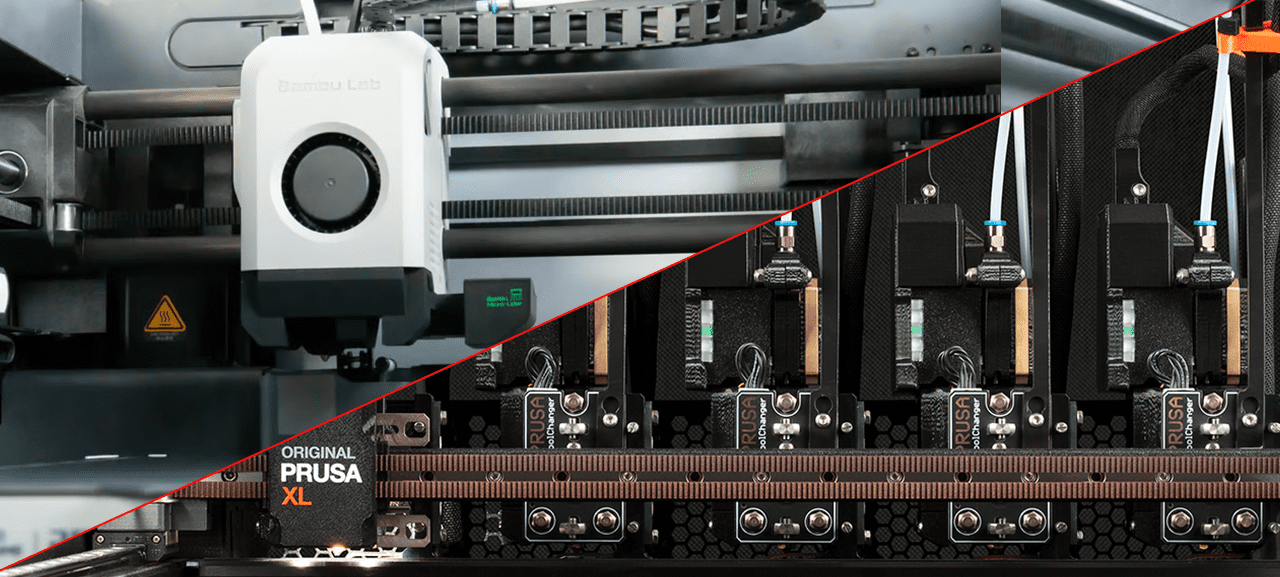
Toolhead Count
Multi-Material (Dedicated Toolheads)
This system utilizes multiple toolheads, each physically mounted on the printer, with independent components such as hotends and extruders. Each toolhead is designated to handle a single filament type or colour. These configurations are common in advanced or professional-grade 3D printers and allow for seamless switching between materials without the need to rely on external mechanisms.
Pros:
- True multi-material support (e.g., PLA + TPU + PVA)
- Eliminates the need for external switching devices
- Improved reliability in filament handling
Cons:
- Increased machine complexity and cost
- Requires precise alignment and calibration of toolheads
- Larger mechanical footprint
Multi-Colour (Single Toolhead + Accessory)
In contrast, this approach relies on a single toolhead, and material switching is handled externally by a separate module or accessory system. This module is typically responsible for either splicing filaments (e.g., Mosaic Palette) or physically switching input filaments (e.g., Prusa MMU or Bambu Lab AMS), all of which feed into a single hotend.
Pros:
- Lower cost and simpler mechanical design
- Smaller, more compact machines
- Easier to maintain a single hotend
Cons:
- Limited to one filament at a time
- Switching times are longer
- Susceptible to wear or mechanical failure in the accessory
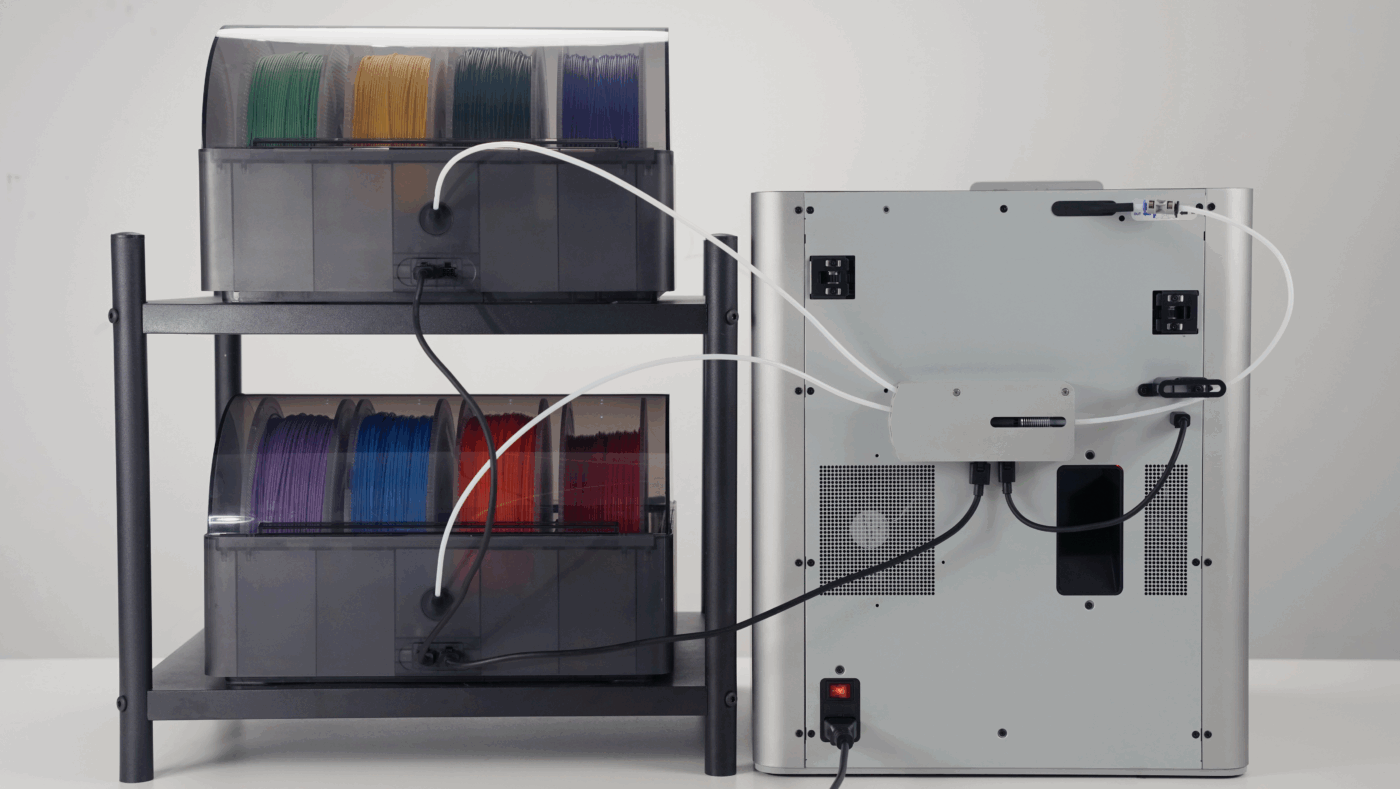
Filament Switching Mechanism
Multi-Material (Independant Extrusion)
Switching filaments in a multi-material setup is independent of any accessory or external device. The printer achieves this by physically moving from one toolhead to another. Since each toolhead is preloaded with its own filament, switching is near-instantaneous and does not involve unloading or loading filaments mid-print. This minimizes downtime and increases reliability.
Pros:
- Immediate switching without unload/load cycles
- Reduces material cross-contamination
- No need for purge blocks in many cases
Cons:
- Increases printhead weight (if not IDEX or toolchanger)
- Mechanical movement and tool parking can increase print time
Multi-Colour (Accessory Dependant)
Filament switching is managed by the accessory, which either selects or splices filaments before feeding them into the printer’s single extruder. This process introduces mechanical complexity and time delays, as it involves retracting the current filament, feeding in the next one, and purging to ensure colour/material purity at the nozzle.
Pros:
- Centralized and modular switching process
- Compatible with standard single-extruder printers (with modification)
- Fewer toolhead movements required
Cons:
- Requires purging to avoid colour mixing
- Complex filament retraction and feeding sequences
- Higher maintenance on switching accessory
Filament Path Length
Multi-Material
The filament path in multi-material printers is generally short, particularly in configurations with direct-drive extruders mounted directly on each toolhead. This direct routing enhances extrusion responsiveness and reduces the likelihood of filament deformation or travel inconsistencies.
Pros:
- Better extrusion accuracy
- Lower likelihood of filament slippage or under-extrusion
- Improved support for flexible materials
Cons:
- Adds weight to the toolhead (for direct-drive)
- Can be harder to service if components are tightly integrated
Multi-Colour
In single-toolhead systems with external accessories, the filament path is considerably longer, extending from the accessory module to the extruder, and then through the hotend. This added length increases the chances of friction, misfeeds, and filament buckling, especially when using flexible filaments.
Pros:
- Keeps the toolhead lightweight
- Accessory can be mounted separately without crowding the gantry
Cons:
- Increased friction and feeding resistance
- Reduced support for flexible filaments (more prone to buckling)
- Difficult to accurately retract or load during transitions
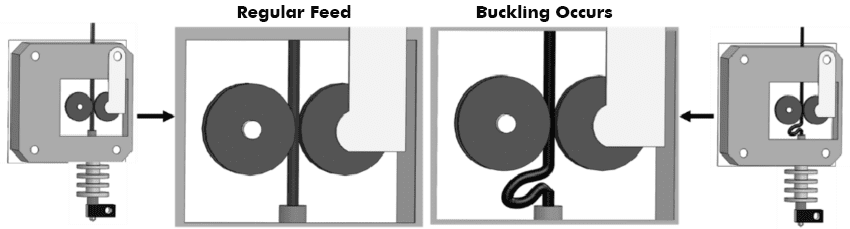
Buckling Risk
Multi-Material
Owing to the short and direct filament paths and the presence of individual extruders per toolhead, the risk of filament buckling is inherently low. This makes the system more tolerant to different filament types, including flexible materials like TPU.
Pros:
- Better for flexible filaments like TPU
- High reliability during complex prints
- Reduced print failures related to feeding
Cons:
- Slightly more prone to jamming if not calibrated correctly (per head)
Multi-Colour
The extended path from the external accessory to the hotend introduces a moderate to high risk of filament buckling, particularly during retraction and reinsertion phases. This is exacerbated when dealing with softer filaments, making such systems less reliable for complex or demanding prints.
Pros:
- Can still print standard materials (PLA, PETG) reliably
- Risk can be reduced with high-quality filament and careful setup
Cons:
- Poor compatibility with soft filaments
- Higher failure rate in complex, long-duration prints
- Difficult to troubleshoot feeding errors mid-print
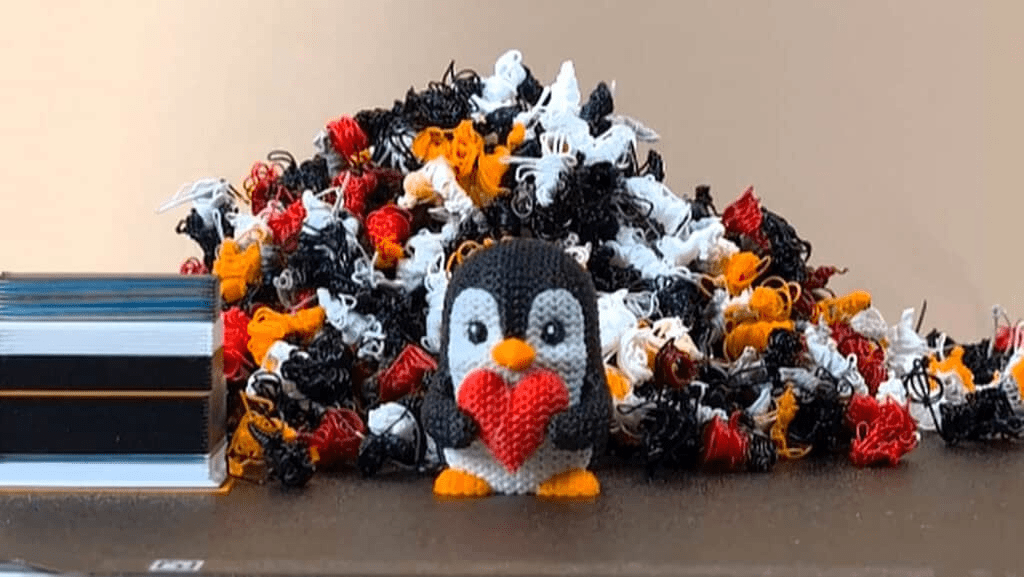
Purge Waste
Multi-Material
Since each toolhead uses a dedicated filament channel, material purging is minimal. Some systems may briefly purge to clean the nozzle tip, but the waste is far less significant than in accessory-based setups.
Pros:
- Efficient material usage
- Faster overall print time
- Environmentally friendlier (less filament waste)
Cons:
- May require occasional wiping or toolhead cleaning mechanisms
Multi-Colour
Material purging is more extensive, as filament residues from the previous colour/material must be completely cleared from the hotend before the next one is extruded. This often requires a purge tower or transition block, which adds to material consumption and print time.
Pros:
- Ensures colour accuracy and reduces contamination
- Predictable transition behavior when calibrated
Cons:
- Significant filament waste (purge towers/blocks)
- Slightly increased print time
- Requires adequate space on the build plate
Prusa XL , Premium Multi-Material Based Model
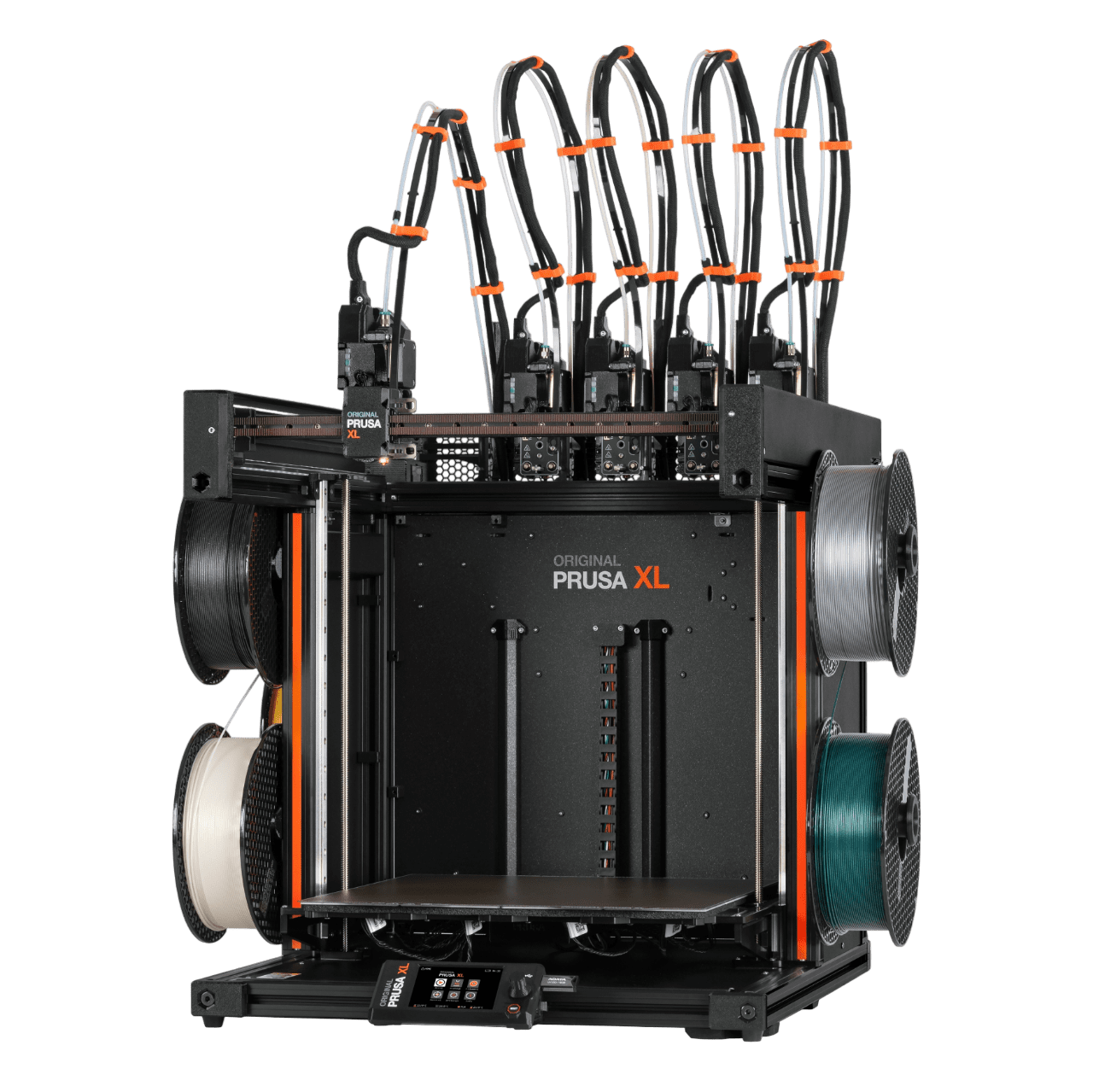
The Prusa XL represents a class of 3D printers designed to print with multiple distinct materials, such as rigid plastics, flexible TPU, or water-soluble support filaments like PVA or BVOH. It achieves this through a tool changer system, allowing up to five independent toolheads, each with its own extruder and hotend.
Unlike multicolor systems that use a single nozzle, the Prusa XL can print entirely different material types in one print. You could, for instance, print a mechanical part in PETG, include soft overmolds in TPU, and use dissolvable PVA for supports, all in one job.
Each toolhead being independent means you avoid issues like stringing, oozing, or residue that happens when changing filaments through a single nozzle system.
Key Features
- Large Build Volume : 360 × 360 × 360 mm build space.
- Maximum Of 5 Toolheads : Enables multi-material, multi-color, or multi-nozzle printing.
- Nextruder with Load Cell Sensor : Integrated load cell for fully automatic first-layer calibration
- Heated Bed with Segmented Zones : Segmented heated bed only heats necessary areas, saving power.
- Multiple Connectivity Options : Control your prints via Touchscreen, Ethernet, USB Stick, Wifi Add On
Printing Specifications:
- Nozzle Temperature: Up to 300°C
- Heatbed Temperature: Up to 120 °C
- Build Volume: 360 × 360 × 360 mm
- Bed Leveling: Automatic mesh bed leveling with Load Cell sensor.
Real-World Applications:
- A robotic gripper with hard mechanical joints and soft fingertips printed simultaneously.
- Snap-fit enclosures that use PETG for structure and TPU for integrated gaskets.
- Architectural scale models or internal channels in engineering parts, printed with PVA supports that dissolve in water.
- A car dashboard mock-up with flexible knobs and rigid housing.
- A jig that uses a hard base for stability and a soft grip to avoid scratching products.
Bambu Lab X1 Carbon, Premium Multi-Colour Based Model
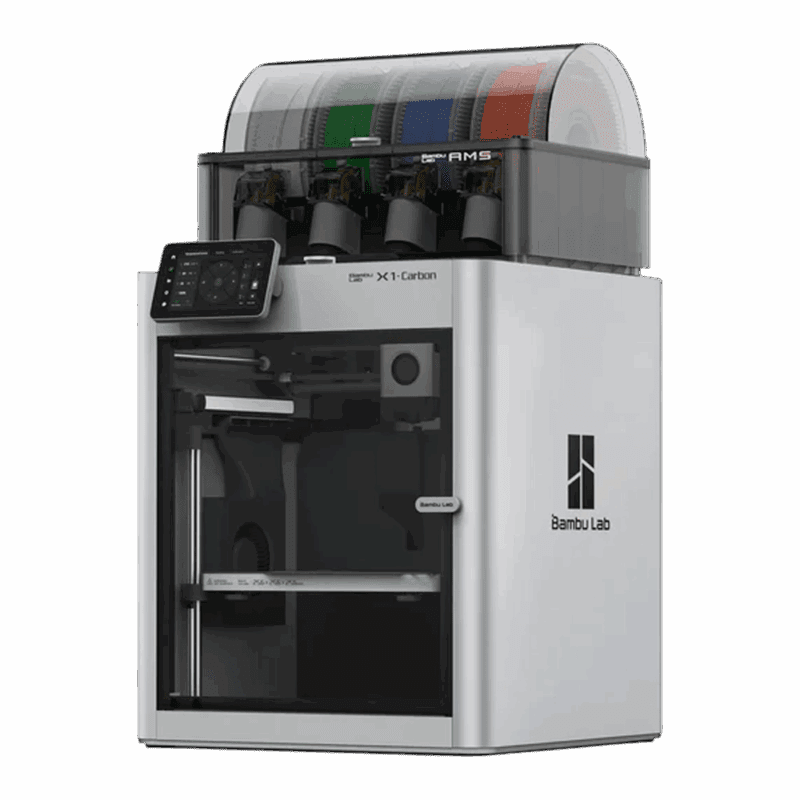
Link: Buy at Smith3D
The Bambu Lab X1 Carbon has been acclaimed for its exceptional material compatibility and advanced features, making it a top choice for hobbyists and professionals alike. Its ease of use, reliability, speed, and quality have set a new standard in the 3D printing industry.
The Automatic Material System (AMS) allows for multi-color and multi-material printing by managing up to four filament spools. It automates filament switching and ensures seamless transitions during prints. Note that while third-party filaments are supported, compatibility with the AMS may vary depending on spool dimensions and materials
Key Features
- Micro Lidar Assisted Bed Leveling : Guarantees micrometer-level precision, enhancing print accuracy and quality.
- Print Resume After Power Outage : Resumes printing seamlessly after power interruptions.
- Unmatched Speed : 20m/s² acceleration cuts print time in half while maintaining a 0.1 mm layer height, delivering speed without compromising on quality.
- Active Vibration Compensation : Improves print quality by counteracting vibrations during printing.
- Multiple Connectivity Options : Control your prints via Bambu Studio, Bambu Handy, SD card, or a local network.
Printing Specifications:
- Nozzle Temperature: Up to 300°C
- Heatbed Temperature: Up to 110 °C
- Build Volume: 256 × 256 × 256 mm
- Bed Leveling: Combines micro Lidar and mechanical sensors for precise leveling
Real-World Applications:
- Multicolor helmets, armor parts, or weapons where painting would be too time-consuming.
- Visual aids where different colors enhance understanding.
- Printing signs, badges, or keychains with corporate branding colors.
- Toys with built-in color detail directly from the printer.
Bambu Lab H2D, Premium Hybrid Based Model
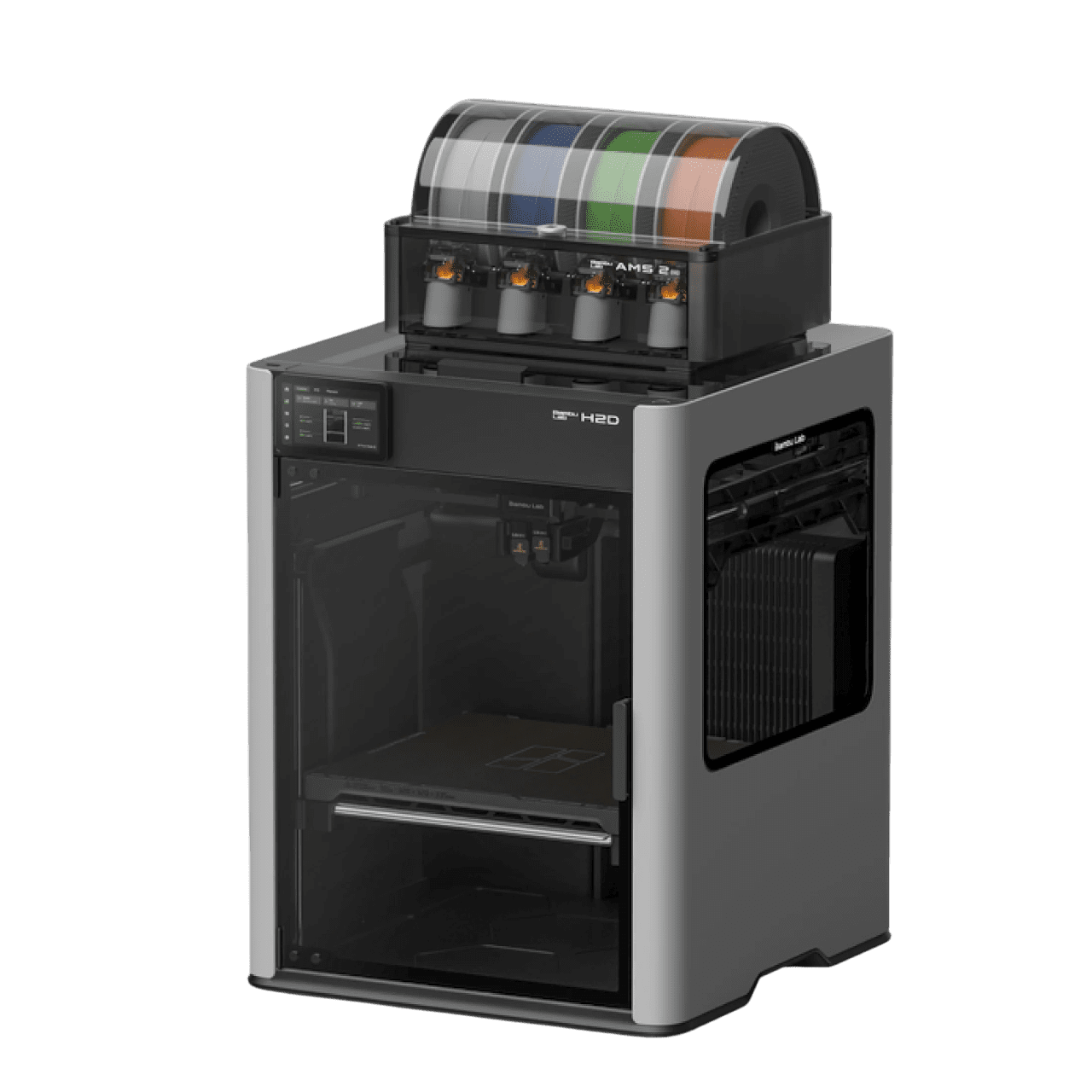
Link: Buy at Smith3D
The Bambu Lab H2D is a versatile, high-performance 3D printer designed for advanced multi-material and multi-colour printing.
The H2D features a dual-nozzle system capable of reaching temperatures up to 350°C, allowing for the printing of diverse materials, including high-temperature and abrasive filaments. Its dual-nozzle system combined with compatibility for multiple AMS units allows for extensive multi-material and multi-color printing.
In an optimal configuration, one hotend can utilize all AMS units while the other uses an external spool holder, enabling up to 25-color printing.
Key Features
- Dual-Nozzle System : Seamless multi-material and multi-color printing with ultra-fast nozzle switching.
- AI-Powered Smart Features : Detects filament buildup, extrusion failures, and material inconsistencies.
- Print Resume After Power Outage : Resumes printing seamlessly after power interruptions.
- Next Gen Speed : 600mm/s print speed with REAL High-Flow Hotend for consistent extrusion.
- Active Vibration Compensation : Active Flow Rate Compensation & Vibration Control for precision printing
- Multiple Connectivity Options : Control your prints via Bambu Studio, Bambu Handy, USB Stick, or a local network.
Printing Specifications:
- Nozzle Temperature: Up to 350°C
- Heatbed Temperature: Up to 110 °C
- Build Volume
- Single Nozzle: 325 × 320 × 325 mm
- Dual Nozzle: 300 × 320 × 325 mm
- Maximum: 350 × 320 × 325 mm
- Bed Leveling: Combines Automatic Mesh Bed Leveling (ABL) and Load Cell Sensor for a more precise levelling.
Practical Examples:
- R&D and Product Development
- Architectural Models with Multi-Color or Multi-Material
- Apparel, Fashion, and Accessories Design
- Tooling and Manufacturing Jigs
- Consumer Product Customization & Print Farm Operations
- Watertight, Heat-Resistant Parts
Conclusion
Choosing the right resin 3D printer depends on your project needs, budget, and the scale of your work. Here’s a quick recap of our top recommendations:
- Prusa XL : Prusa XL offers a true multi-material printing solution, ideal for professional or industrial users. With each toolhead handling its own filament, switching is fast and reliable without material cross-contamination.
- Bambu Lab X1C : The X1C relies on its external accessory, AMS, to feed multiple filaments into a single hotend. It’s more accessible and cost-effective but involves compromises in reliability and print speed.
- Bambu Lab H2D : The H2D combines the best of both worlds with two independent nozzles and AMS filament automation, delivering multi-material functionality with minimal compromise. It integrates performance, convenience, and automation in one platform.
At Smith3D, we offer a wide range of 3D printers and accessories to suit all your printing needs. Smith3D also offers a variety of resin materials, perfect for different types of projects. Whether you’re just starting out or looking to upgrade your setup, our team is here to help you find the best solu
Need Help?
Contact our team at +(60)10-344 3128 or sales@smith3d.com for personalized assistance with your project. Our technical experts are ready to help you make the best choice for your specific needs.
Where to Buy These 3D Printers
Bambu Lab X1 Series – X1 Carbon | X1 Carbon Combo AMS X1CC X1C
Price range: RM5,199.00 through RM7,499.00Bambu Lab H2D
Price range: RM9,499.00 through RM15,999.00